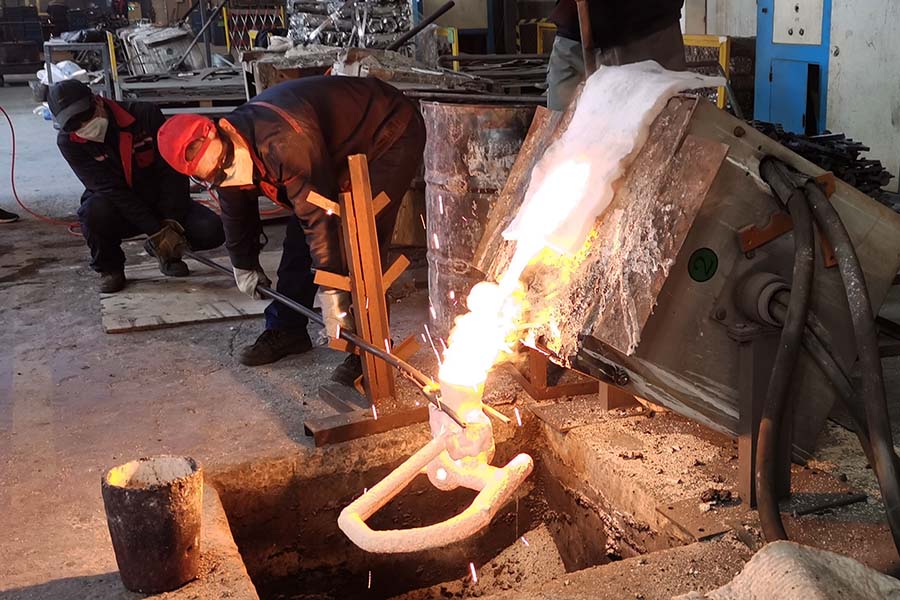
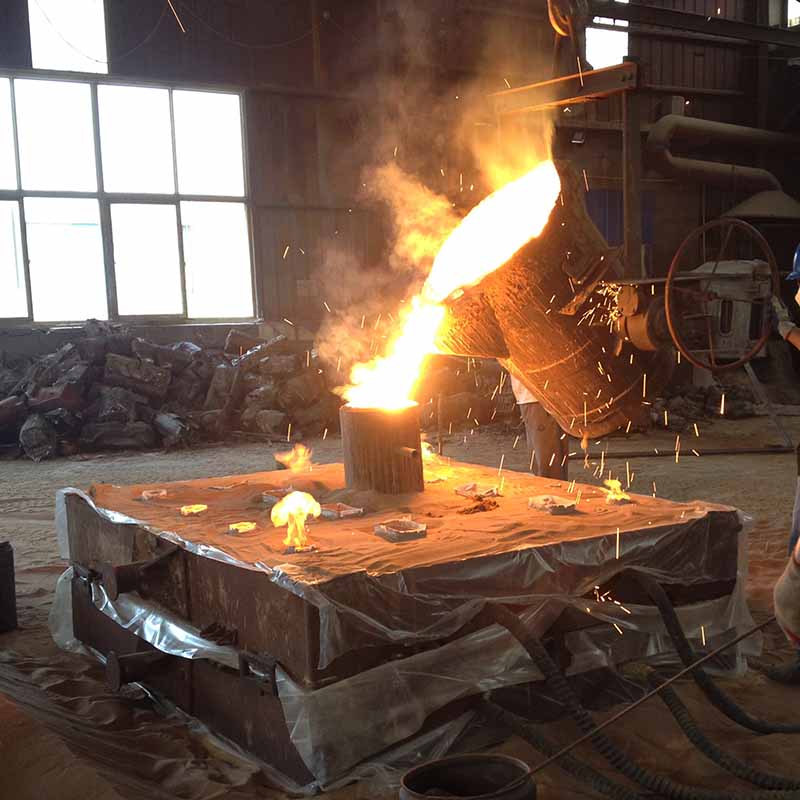
Gieten is een van de vroegste metaalvormmethoden die de mens kent. Het betekent over het algemeen het gieten van gesmolten metaal in een vuurvaste mal met een holte in de vorm die moet worden gemaakt, en het laten stollen ervan. Wanneergestold, wordt het gewenste metalen voorwerp uit de vuurvaste mal gehaald, hetzij door de mal te breken, hetzij door de mal uit elkaar te halen. Het gestolde voorwerp wordt gieten genoemd. Dit proces wordt ook wel gieten genoemd, en de moderne fabriek die zich richt op het gieten van metalen onderdelen heetgieterij.
1. Geschiedenis van het gietproces
Het gietproces werd waarschijnlijk rond 3500 voor Christus ontdekt in Mesopotamië. In veel delen van de wereld werden in die periode koperen bijlen en andere platte voorwerpen uitgedraaid in open mallen van steen of gebakkenklei. Deze mallen bestonden hoofdzakelijk uit één stuk. Maar in latere perioden, toen er ronde voorwerpen gemaakt moesten worden, werden dergelijke mallen in twee of meer delen gesplitst om het terugtrekken van de ronde voorwerpen te vergemakkelijken.De bronstijd (ca. 2000 voor Christus) bracht veel meer verfijning in het gietproces. Misschien werd voor het eerst een kern uitgevonden om holle zakken in de voorwerpen te maken. Deze kernen waren gemaakt van gebakken klei.Ook werd het cire perdue- of verloren wasproces op grote schaal gebruikt voor het maken van ornamenten en fijn werk.
De giettechnologie is vanaf ongeveer 1500 voor Christus sterk verbeterd door de Chinezen. Voordien is er geen bewijs gevonden van enige castingactiviteit in China. Ze lijken niet geweldig te zijn geweestHij was bekend met het cire perdue-proces en gebruikte het niet op grote schaal, maar specialiseerde zich in plaats daarvan in meerdelige mallen voor het maken van zeer ingewikkelde klussen. Ze hebben veel tijd besteed aan het perfectioneren van de mal tot in het kleinste detail, dus dat nauwelijksAan het gietstuk uit de mallen was nog enige afwerking nodig. Waarschijnlijk maakten ze stukmallen met daarin zorgvuldig passende stukken, in totaal dertig of meer. Er zijn zelfs veel van dergelijke schimmels opgegraventijdens archeologische opgravingen in verschillende delen van China.
De beschaving van de Indusvallei staat ook bekend om het uitgebreide gebruik van koper en brons voor ornamenten, wapens, gereedschappen en gebruiksvoorwerpen. Maar er was niet veel verbetering in de technologie. Van de variOndanks de objecten en beeldjes die werden opgegraven op de locaties in de Indusvallei, lijken ze bekend te zijn met alle bekende gietmethoden, zoals open mal, stukvorm en het cire perdue-proces.
Hoewel India de uitvinding van smeltkroesstaal zou kunnen worden toegeschreven, was er in India niet veel zichtbaar van ijzergieterij. Er zijn aanwijzingen dat het ijzergieten rond 1000 voor Christus in Syrië en Perzië was begonnen. Het lijktDatijzergietentechnologie in India wordt al gebruikt sinds de invasie van Alexander de Grote, rond 300 voor Christus.
De beroemde ijzeren pilaar die zich momenteel vlakbij de Qutb-minar in Delhi bevindt, is een voorbeeld van de metallurgische vaardigheden van de oude Indianen. Het is 7,2 m lang en is gemaakt van puur smeedbaar ijzer. Aangenomen wordt dat dit van deperiode van Chandragupta II (375-413 n.Chr.) van de Gupta-dynastie. De roestsnelheid van deze pilaar, die buiten in de open lucht staat, is vrijwel nul en zelfs het begraven gedeelte roest extreem langzaam. Ditmoet eerst zijn gegoten en vervolgens in de uiteindelijke vorm zijn gehamerd.
2. Voordelen en beperkingen
Het gietproces wordt veelvuldig gebruikt bij de productie vanwege de vele voordelen. Gesmolten materiaal stroomt in elk klein gedeelte van de vormholte en als zodanig in elke ingewikkelde vorm – internof extern – kan worden gemaakt met het gietproces. Het is mogelijk om vrijwel elk materiaal te gieten, zowel ferro als non-ferro. Verder zijn de noodzakelijke gereedschappen die nodig zijn voor het gieten van mallen zeer eenvoudiggoedkoop. Hierdoor is het voor proefproductie of productie van een kleine partij een ideale methode. Bij het gietproces is het mogelijk om de hoeveelheid materiaal precies daar te plaatsen waar het nodig is. Als resultaatgewichtsreductie in ontwerp kan worden bereikt.Gietstukkenworden over het algemeen gelijkmatig van alle kanten gekoeld en daarom wordt verwacht dat ze geen richtingseigenschappen hebben. Er zijn bepaalde metalen en legeringendie alleen kan worden verwerkt door gieten en niet door enig ander proces zoals smeden vanwege metallurgische overwegingen. Gietstukken van elk formaat en gewicht, zelfs tot 200 ton, kunnen worden gemaakt.
De maatnauwkeurigheid en oppervlakteafwerking worden echter normaal bereiktzandgietproceszou in veel gevallen niet geschikt zijn voor definitieve toepassing. Om met deze gevallen rekening te houden, een speciale castingEr zijn processen zoals spuitgieten ontwikkeld, waarvan de details in latere hoofdstukken worden gegeven. Bovendien is het zandgietproces tot op zekere hoogte arbeidsintensief en daarom zijn er veel verbeteringen op gericht.zoals machinaal gieten en gieterijmechanisatie. Bij sommige materialen is het vaak moeilijk om gebreken, die voortkomen uit het daarin aanwezige vocht, te verwijderenzand gietstukken.
3. Castingvoorwaarden
In de volgende hoofdstukken worden de details van het zandgieten besproken, wat het basisproces van het gieten vertegenwoordigt. Voordat we op de details van het proces ingaan, zouden we eerst een aantal woorden uit de gietwoordenschat moeten definiërengepast.
Kolf– Een vormkolf is een vormkolf die de zandvorm intact houdt. Afhankelijk van de positie van de fles in de malstructuur, wordt deze met verschillende namen aangeduid, zoals drag, cop en Wang. Het is gemaakt van houtvoor tijdelijke toepassingen of meer in het algemeen van metaal voor langdurig gebruik.
Sleuren– Onderste vormkolf
Omgaan met– Bovenste vormkolf
Wang– Tussenvormkolf gebruikt bij driedelig gieten.
Patroon– Patroon is een replica van het uiteindelijke object dat met enkele aanpassingen moet worden gemaakt. Met behulp van het patroon wordt de vormholte gemaakt.
Scheidingslijn– Dit is de scheidslijn tussen de twee vormkolven waaruit de zandvorm bestaat. Bij een splitpatroon is het tevens de scheidslijn tussen de twee helften van het patroon
Onderste bord– Dit is een plank die normaal gesproken van hout is gemaakt en die wordt gebruikt bij het begin van het maken van de mallen. Het patroon wordt eerst op de onderplank gehouden, er wordt zand op gestrooid en daarna wordt er in de sleep geramd.
Tegenover zand– De kleine hoeveelheid koolstofhoudend materiaal dat op het binnenoppervlak van de vormholte wordt gestrooid om een betere oppervlakteafwerking aan de gietstukken te geven
Vormzand– Het is het vers bereide vuurvaste materiaal dat wordt gebruikt voor het maken van de vormholte. Het is een mengsel van silicaklei en vocht in de juiste verhoudingen om de gewenste resultaten te verkrijgen en het omringt depatroon tijdens het maken van de mal.
Steunzand– Het is het grootste deel van het vuurvaste materiaal dat in de mal wordt aangetroffen. Dit bestaat uit gebruikt en verbrand zand.
Kern– Het wordt gebruikt voor het maken van holle holtes in gietstukken.
Gietbak– Een kleine trechtervormige holte bovenaan de mal waarin het gesmolten metaal wordt gegoten.
Spoor– De doorgang waardoor het gesmolten metaal uit de gietbak de vormholte bereikt. In veel gevallen regelt het de metaalstroom in de matrijs.
Loper– De doorgangen in het scheidingsvlak waardoor de stroom gesmolten metaal wordt geregeld voordat deze de vormholte bereikt.
Hek– Het daadwerkelijke toegangspunt waarlangs gesmolten metaal de vormholte binnendringt.
Rozenhoedje– Chaplets worden gebruikt om kernen in de vormholte te ondersteunen om voor het eigen gewicht te zorgen en de metallostatische krachten te overwinnen.
Chill– Koude rillingen zijn metalen voorwerpen die in de mal worden geplaatst om de koelsnelheid van gietstukken te verhogen en zo een uniforme of gewenste koelsnelheid te verkrijgen.
Verhoger– Het is een reservoir met gesmolten metaal dat in het gietstuk wordt aangebracht, zodat heet metaal terug in de vormholte kan stromen wanneer het metaalvolume door stolling afneemt
4. Procedure voor het maken van zandvormen
De procedure voor het maken van een typische zandmal wordt in de volgende stappen beschreven:
Eerst wordt een onderplaat op het vormplatform of op de vloer geplaatst, waardoor het oppervlak egaal wordt. De sleepvormkolf wordt ondersteboven op de bodemplaat gehouden, samen met het sleepgedeelte van depatroon in het midden van de fles op het bord. Er moet voldoende ruimte zijn tussen het patroon en de wanden van de kolf, die in de orde van 50 tot 100 mm moet liggen. Er wordt droog gevelzand overheen gestrooidhet bord en het patroon om een niet-plakkerige laag te creëren. Vers bereid vormzand van de vereiste kwaliteit wordt nu in de sleep en op het patroon gegoten tot een dikte van 30 tot 50 mm. De rest van de sleepfles welvolledig gevuld met het steunzand en gelijkmatig geramd om het zand te verdichten. Het aanstampen van het zand moet op de juiste manier gebeuren om het niet te hard te verdichten, waardoor het ontsnappen van gassen moeilijk wordt.en ook niet te los, zodat de mal niet voldoende sterkte zou hebben. Nadat het stampen voorbij is, wordt het overtollige zand in de kolf volledig geschraapt met een platte staaf tot ter hoogte van de kolfranden.
Nu worden met een ontluchtingsdraad, een draad met een diameter van 1 tot 2 mm en een puntig uiteinde, ontluchtingsgaten gemaakt in de weerstand tot de volledige diepte van de kolf en tot aan het patroon om de verwijdering van gassen te vergemakkelijken tijdens het gietenverharding. Hiermee is de voorbereiding van de sleep voltooid.
De voltooide sleepfles wordt nu naar de onderste plank gerold, waardoor het patroon zichtbaar wordt zoals weergegeven op de foto. Met behulp van een slick worden de zandranden rondom het patroon gerepareerd en wordt de kaphelft van het patroon eroverheen gelegdhet sleeppatroon, uitlijnen met behulp van paspennen. De kolffles bovenop de sleep wordt weer uitgelijnd met behulp van de pinnen. Het droge scheidingszand wordt over de sleep en op het patroon gestrooid.
Op een kleine afstand van ongeveer 50 mm van het patroon bevindt zich een aanspuitpen voor het maken van de aanspuitdoorgang. Ook wordt de stijgpin indien nodig op een geschikte plaats bewaard en wordt vers bereid vormzand vergelijkbaarvan de sleep wordt samen met het steunzand gestrooid. Het zand wordt grondig geramd, overtollig zand geschraapt en overal in de kap worden ventilatiegaten gemaakt, net als bij de sleep.
De aanspuitpen en de e-stijgpen worden voorzichtig uit de kolf getrokken. Later wordt de gietbak nabij de bovenkant van de spruw uitgesneden. De trekhaak is gescheiden van de sleep en eventueel los zand op de trek- en sleepinterfacevan de weerstand wordt met behulp van een balg weggeblazen. Nu worden de helften van het trekpatroon en de sleeppatroon teruggetrokken door gebruik te maken van de trekpinnen en het patroon rondom te kloppen om de malholte enigszins te vergroten, zodat deschimmelwanden worden niet aangetast door het terugtrekkende patroon. De lopers en de poorten worden zorgvuldig in de mal gesneden zonder de mal te bederven. Overtollig of los zand dat in de lopers en de vormholte wordt aangetroffen, wordt geblazenweg met behulp van de balg. Nu wordt het bekledingszand in de vorm van een pasta over de gehele vormholte en de lopers aangebracht, waardoor het voltooide gietstuk een goede oppervlakteafwerking krijgt.
Met behulp van een kernkast wordt een droge zandkern voorbereid. Na geschikt bakken wordt het in de vormholte geplaatst, zoals weergegeven op de foto. De kap wordt op de sleep vervangen en zorgt voor de uitlijning van de twee door middel van depinnen. Er wordt een geschikt gewicht op het handvat gehouden om te zorgen voor de opwaartse metallostatische kracht tijdens het gieten van gesmolten metaal. De mal is nu, zoals weergegeven op de foto, klaar om te gieten.
Posttijd: 25 december 2020